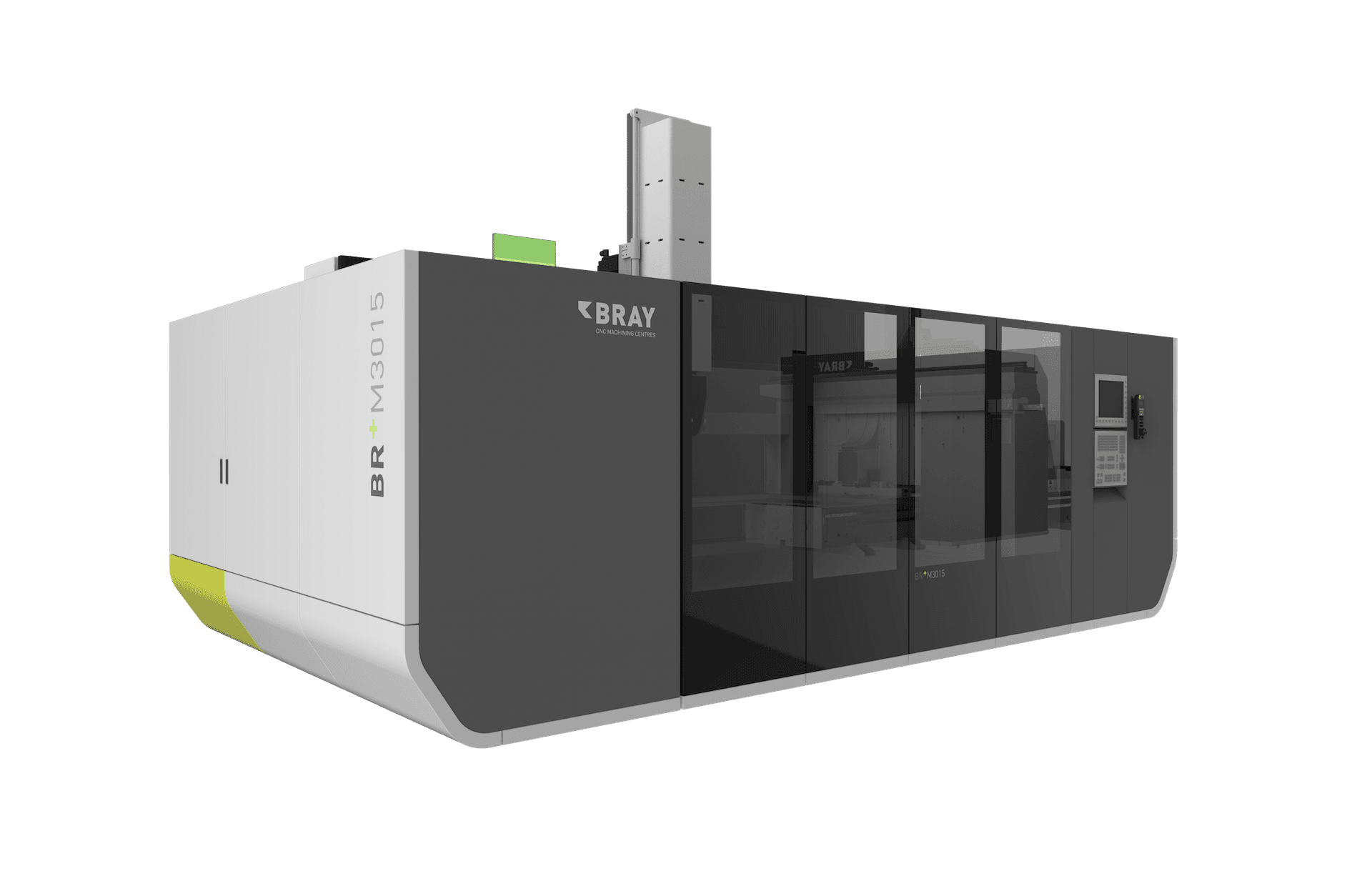
Introduction Additive manufacturing techniques like 3D printing and vacuum casting enable companies to produce functional plastic prototypes, end use parts, tooling, and fixtures without the high cost of machining or injection molding hard tooling. However, understanding key differences between “3D printing” and “vacuum casting” processes enables properly leveraging the advantages of each to match application needs in terms of accuracy, material options, volumes capabilities, secondary operations, project speed and more.
This comprehensive guide examines typical use cases plus compares popular materials, tolerance capabilities, production volumes suitability, lead times, finishing needs and overall costs between 3D printing and vacuum casting processes. Matching part requirements and specifications to process strengths ensures manufacturing success.
Typical Applications Suited to Each Process Before diving into technical comparisons, it helps to understand where 3D printing and vacuum casting are typically used:
3D Printing Use Cases
- Prototyping form, fit, function
- Low volume end use parts
- Customized tooling and fixtures
- Lightweight aerospace and motorsports components
Vacuum Casting Use Cases
- Appearance models/master patterns – autos, consumer goods
- Bridge tooling with moderate production runs
- Low volume parts requiring tighter tolerances
- Short run injection molding without hard tooling
These applications take advantage of core strengths unique to each process.
Popular Material Options Comparison The materials compatible with 3D printing vs vacuum casting differs considerably based on how each process works to build or mold components layer-by-layer or via injected resin reactants.
3D Printing Materials
- Production grade thermoplastics – ABS, PC, Nylon
- Photopolymers and epoxy resins
- Flexible and rubber-like materials
- Metals – stainless steel, aluminum, titanium alloys
Vacuum Casting Materials
- Polyurethane resins – range of durometers
- Silicone rubbers – shore ranges from very soft to durable
- Other platinum cure silicone materials
Part accuracy, visual appearance, environmental stability and mechanical performance requirements will determine suitable material selection.
Tolerance Capability Comparison
A key differentiator between additive manufacturing and vacuum casting is achievable accuracy relative to an original CAD model. Precision relates closely to intended application – prototyping, mass production, etc.
Dimensional Accuracy Ranges
- 3D Printing: ± 0.5-0.7% (~500 microns per 100mm)
- Vacuum Casting: ± 0.2-0.4% (~200 microns per 100mm)
While ranges overlap, vacuum casting generally produces tighter tolerances useful for master patterns or short run production where function is critical. 3D printing fits lower precision requirements.
Understanding accuracy needs is essential to match right process capabilities.
Volume Suitability Comparison 3D printing and vacuum casting processes also differ considerably regarding suitable production quantities based on per piece process economics.
Typical Volume Ranges
- 3D Printing: 1-1,000 units
- Vacuum Casting: 25-25,000+ units
Lead times, changeover, and material costs also factor in here. Small batches under 25 pieces favor 3D printing while outputs beyond 1,000 units warrant hard tooling. Vacuum casting hits the sweet spot inbetween.
Lead Time Comparison How quickly components can be produced also varies greatly between additive vs mold-based processes.
Lead Time Ranges
- 3D Printing: Hours to days
- Vacuum Casting: Days to weeks
3D printing enables fast turnaround for prototypes or critical replacement components with very little ramp up. Vacuum casting requires mold fabrication based on master patterns so takes longer for initial parts but then offers faster cycle times at volume.
Understanding speed considerations is vital where products have compressed development cycles or production gaps need bridging during manufacturing transitions.
Secondary Machining Comparison Any supplementary finishing or processing needs should also factor into assessing suitability between 3D printing and vacuum casting options.
Post Processing Needs
- 3D Prints: Support removal, sanding, coating/painting
- Vacuum Casts: Flash removal, polishing, pad printing decorating
As with any manufacturing process, planning secondary operations in advance allows efficiency through the full production sequence.
Cost Profile Comparisons Upfront per unit economics can steer designers and engineers toward different rapid manufacturing technologies.
Cost Considerations
- 3D printing equipment costs lower
- Vacuum casting has higher mold fabrication costs
- 3D printing more economical for singles or very low volumes
- Vacuum casting cheaper per piece at moderate volumes
- Part size impacts mold fabrication and material costs
Conclusion This detailed 3D printing vs vacuum casting comparison reveals unique advantages of both processes across accuracy requirements, material limitations, volume capabilities and secondary finishing needs. Matching specifications to process strengths and cost profiles ensures selecting the optimal rapid manufacturing technology for each new product development need. Work closely with competent suppliers to validate approaches that maximize quality, control cost and accelerate speed to market goals.

Tech Hub Digital, a one-stop destination for complete technology-related information.