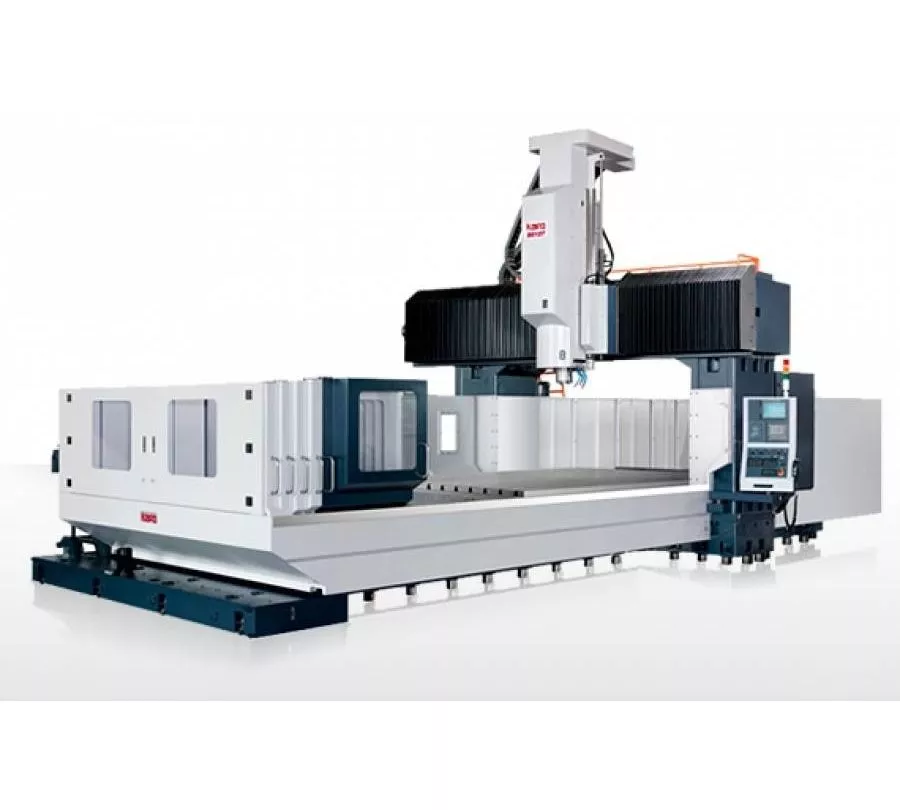
Injection molding using premium plastics like polycarbonate and ABS allows manufacturers to produce durable, functional parts with complex geometries across unlimited industries – from automotive lenses to consumer electronics enclosures and medical devices. These versatile thermoplastics each offer unique performance advantages but also differ in how they must be processed.
Understanding key distinctions between “polycarbonate injection molding” and “ABS injection molding” processes enables properly matching each material’s strengths to application needs as well as informing mold design and production decisions. Durable products can be manufactured via thermoplastic molding with polycarbonate resins.
This comprehensive guide examines popular uses plus advantages of each resin and dives into processing comparisons around molding parameters, tooling, shrinkage rates, secondary machining needs, and more. Injection molded ABS plastics are commonly used for consumer electronics housings and automotive parts.
Typical Applications Suited to Each Plastic
Before covering molding processes, it helps to understand typical applications leveraging PC and ABS today:
Polycarbonate Use Cases
- Impact resistance needed – protective gear, shields
- Transparency combined with durability – lenses, covers
- Autoclavable medical components – labware, fluidics
- Electrical insulation applications – connectors, casings
ABS Use Cases
- Consumer electronics housing – appliances, laptops
- Automotive interiors and light housings
- Medical enclosures and instrument bodies
- Toys and sporting goods needing rigidity
These applications capitalize on inherent advantages offered by each thermoplastic.
Polycarbonate vs ABS Material Properties Compared How suitable a plastic performs under injection molding stems from inherent mechanical, thermal, and chemical properties. Polycarbonate and ABS excel in similar applications but achieve such performance through different property strengths.
Polycarbonate
- Extreme impact resistance and ductility
- Transparent with light diffusion abilities
- Heat and autoclave sterilizable
- Naturally flame retardant with high heat deflection
ABS
- High rigidity and tensile strength
- Nice aesthetic finishes and colorability
- Good chemical resistance
- Cost effective relative to engineering resins
Understanding these core strengths appropriately matches opportunities to resin that will achieve required physical performance.
Now we examine how these materials actually transform under injection molding processes.
Molding Parameter Comparison Because polycarbonate and ABS reactants differently when exposed to heat, pressure, and flow inside the injection barrel, molding process set points differ considerably between resins to produce high quality, defect-free outputs.
Key Process Differences:
Parameter | Polycarbonate | ABS |
---|---|---|
Processing Temp | ~300-360°C | ~200-260°C |
Mold Temps | ~80-120°C | ~40-60°C |
Injection Pressure | Medium-High | Medium |
Clamp Tonnage | High | Medium |
Fill Times | Intermediate | Very fast |
Cooling Times | Slow | Fast |
These set points impact parameters like tool design, equipment capabilities required, overall cycle times, part aesthetics, and downstream operations needed.
Understanding variances here allows properly equipping production lines and tuning processes that play to each plastic’s unique molding behaviors.
Tooling Considerations Mold components and features must also be tailored to a given resin’s characteristics under high temperature filling, packing, and cooling phases of injection cycles.
Tooling Differences:
Feature | Polycarbonate | ABS |
---|---|---|
Vent Depth | Shallow | Moderate |
Draft Angles | Higher | Standard |
Ejection Pins | Generous | Standard |
Cooling Lines | Dense | Moderate |
Polishing | Higher | Optional |
These mold geometries and components compensate for material properties during molding. For example, shallower vents prevent splashing of low viscosity PC while stronger ABS readily flows into deeper channels.
Understanding tooling criteria upfront ensures molds deliver required production volumes without defects.
Shrinkage Rate Variances How much molded plastic parts shrink as they cool down to room temperature depends on the resin used. This must be accounted for when dimensioning final mold cavity and core geometries.
Shrinkage Comparison:
- Polycarbonate: ~0.5-0.7%
- ABS: ~0.3-0.8%
While ranges overlap, polycarbonate averages lower shrinkage than ABS. However, factors like fill rates, part thicknesses, gate locations influence shrinkage so must be confirmed through mold flow simulations to size molds precisely.
Secondary Machining Needs Any secondary CNC machining, drilling, tapping, decorating needs vary considerably between plastics based on machinability, edge finishing, solvent bonding, and chemical etching behaviors.
Post-Molding Considerations:
Operation | Polycarbonate | ABS |
---|---|---|
Drilling | Challenging | Very Easy |
Routing | Brittle Edges | Clean Cuts |
Pad Printing | Low Adhesion | Excellent |
Vapor Polishing | Compatible | Incompatible |
ABS works very well across most secondary machining but PC requires more nuanced processes. Prospective applications driving such downstream operations plays into material selection.
Conclusion This detailed comparison of popular “polycarbonate injection molding” and “ABS injection molding” processes reveals the advantages of each along with how to optimize molding production based on unique filler properties. Matching part geometries, tooling strategies, process parameters and secondary machining needs to the resin best meeting mechanical performance, budget and application goals ensures manufacturing success. Work closely with your injection molder and mold maker to plan how to best leverage PC vs ABS strengths for your next plastic component project.

Tech Hub Digital, a one-stop destination for complete technology-related information.