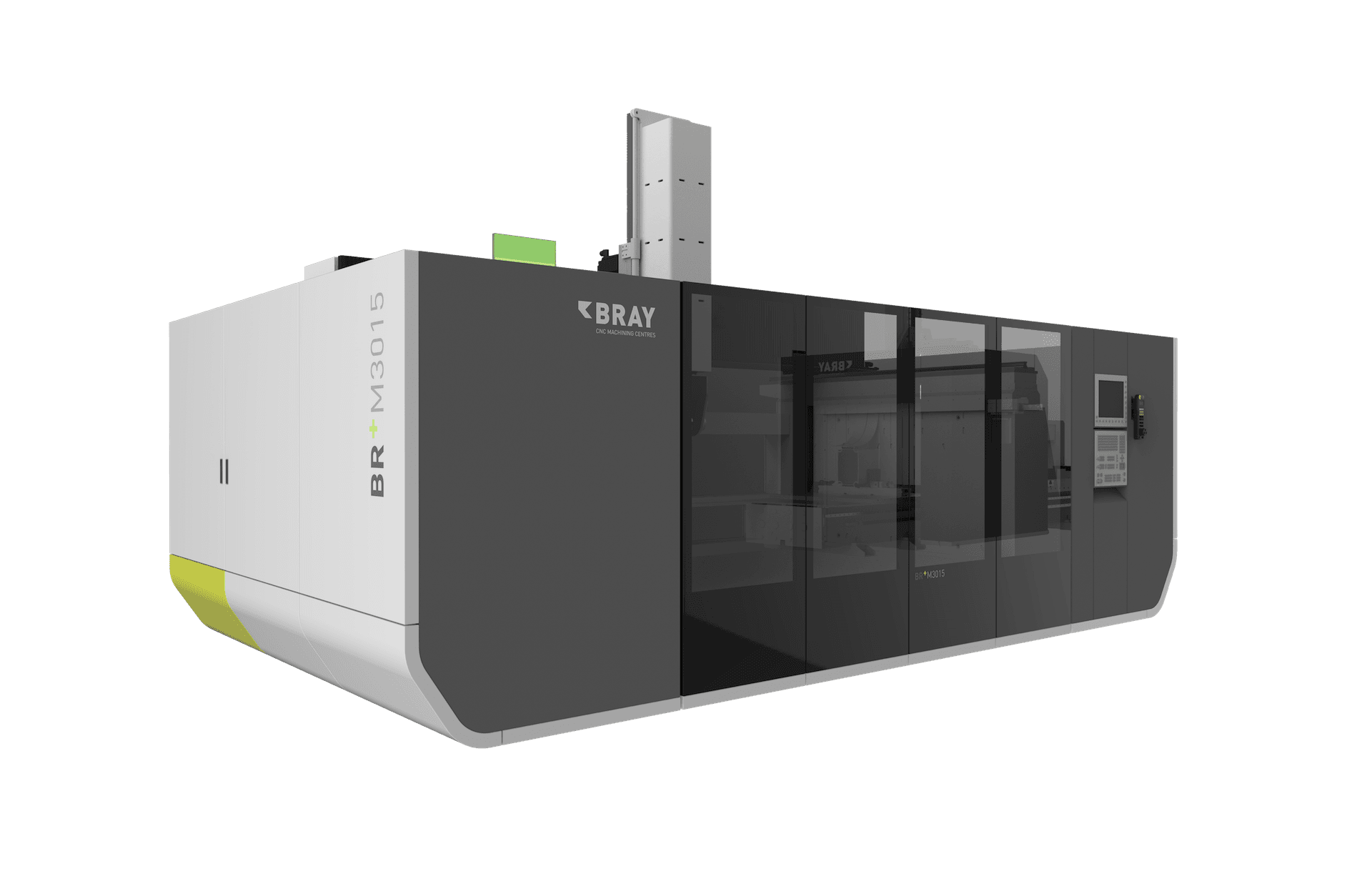
Introduction Injection plastic molds are essential tooling used to mass produce plastic products and component parts for nearly every industry imaginable. As global manufacturing has shifted, China has become the epicenter for complex, highly precise molds and dies due to its mature infrastructure, skilled workforce, and capacity capabilities. Overseas companies today heavily rely on Chinese suppliers for molds like “battery case moulds” and “paint bucket moulds” used to produce plastic enclosures and containers on an industrial scale.
However, navigating China’s vast mold building landscape and ensuring high quality tools are produced requires knowledge around properly vetting and partnering with legit factories, overseeing production, conducting quality assurance, and managing international shipping. Injection molds for producing battery enclosures can be custom made to specification.
This guide shares professional advice for overseas buyers procuring custom battery case or paint bucket molds from China’s manufacturing ecosystem. Follow these best practices to streamline sourcing and achieve precision engineered molds without defects.
Selecting Reliable Chinese Mold Makers With tens of thousands of mold factories in China, identifying legit, experienced, and capable partners emerges as the first hurdle for international buyers. However, taking a systematic approach to supplier selection makes this manageable. Plastic pails used for industrial paint containment are manufactured using dedicated molds.
Aspects to scrutinize when assessing a prospective custom mold producer include:
- Years in business and staff skill levels
- Range of molds fabricated previously
- Production technology and machining capabilities
- Quality control certifications obtained
- Volume output capacity levels
- Previous client industries and feedback
- English language proficiency
Ideally you would audit top factories in-person if traveling to China. If not an option, third-party sourcing agents can conduct onsite evaluations per your criteria and preferences.
Verifying strong client references and testimonials also builds confidence in mold maker expertise before engagement.
Defining Precise Mold Specifications Providing clear, technical molded product and mold requirements to prospective factories is crucial for Chinese teams to properly estimate pricing, production timelines, and project feasibility. The more detailed the upfront specifications, the less chance of downstream misalignments.
Critical mold particulars to supply suppliers include:
- Target mold dimensions and configurations
- Required part geometry, draft angles, positional tolerances
- Output expectations – cycle times, cavitation, shot process parameters
- Material being molded – Important for shrinkage, flow dynamics, etc.
- Any special construction details or secondary operations required
- Testing needs and quality control expectations
Additional mold criteria will refine quoting but above factors have largest impact in costing estimation and project planning.
ExecutingQuality Management Best Practices Close partnership directly with your chosen Chinese mold producer or intermediary manager enables quality oversight through the entire custom mold fabrication process.
Recommended phases to track and inspect include:
1. Design Finalization Review initial 3D renderings and mold flow simulations. Have designer walk through choices on venting, runner layouts, action sequences, etc. Provide refinement feedback.
2. Tool Production
Periodic check-ins ensure proper CNC machining, grinding, EDM work. If possible, visit the factory to monitor build.
3. Sampling & Testing Conduct test shots to verify plastic part quality relative to product needs – check dimensions, texture, functional performance, etc. Refine tool as required.
4. Pilot Production
Approve small pilot batch before full production ramp up. Spot check samples dimensional accuracy, cosmetics, minor adjustments needed, etc.
Staying engaged throughout mold engineering and fabrication stages prevents major defects from appearing in finished tools.
Arranging International Shipping & Logistics Navigating basics like export packaging, customs clearance, bonded warehousing, and ocean/air shipping will be required to bring your finished Chinese molds or subsequent molded parts back to your home country.
Key considerations around international logistics:
- Properly crate large molds to prevent damage
- Work with freight forwarders familiar with mold shipping
- Simplify imports by providing necessary paperwork for customs
- Choose cost-effective carrier based on delivery urgency
- Have post-delivery warehouse storage or brokerage solution in place
Reliable Chinese suppliers have expertise to advise on reliable shipping pipelines. Just communicate what import logistics you must handle upon arrival to prevent port storage fees or customs delays.
Conclusion Sourcing molds like battery cases or paint buckets from China offers tremendous access to world-class quality and cost savings but still requires diligence when selecting partners and liasing for quality. Use the above guide covering supplier vetting, spec alignment, quality control, and shipping logistics as a blueprint when looking to purchase your custom molds out of China. Finding a capable, communicative factory makes accessing China’s manufacturing strengths much simpler for overseas buyers requiring precision plastic mold tooling.

Tech Hub Digital, a one-stop destination for complete technology-related information.