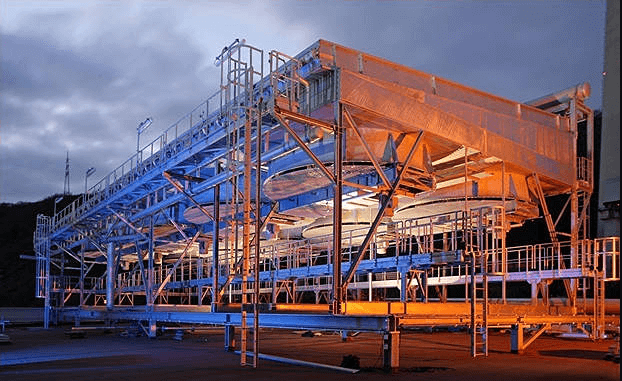
Heat exchangers play a crucial role in various industries, facilitating the transfer of heat between two or more fluids. In this comprehensive guide, we will delve into two prominent types of heat exchangers: Fin Fan Heat Exchangers and Shell and Tube Heat Exchangers.
Understanding Fin Fan Heat Exchangers
Fin Fan Heat Exchangers, also known as air-cooled heat exchangers, are integral components in various industrial processes. Understanding their design, functionality, and advantages is crucial for optimizing their usage in diverse applications.
How Fin Fan Heat Exchangers Work
- Basic Principle
- Fin Fan Heat Exchangers operate on the principle of convective heat transfer. Heat dissipation occurs through the exchange of thermal energy between the process fluid inside the tubes and the ambient air outside.
- Fin Design
- The unique design feature of finned surfaces significantly enhances the heat transfer efficiency. Fins, resembling blades or louvers, extend from the tubes into the surrounding air, providing a larger surface area for heat exchange.
- Air Circulation
- The heat dissipation process relies on natural or forced air circulation. In natural draft configurations, the buoyancy of hot air naturally draws cooler air over the finned surfaces. In forced draft setups, fans actively propel air across the fins for more controlled cooling.
Advantages of Fin Fan Heat Exchangers
- Suitability for Outdoor Installations
- One of the primary advantages of Fin Fan Heat Exchangers is their suitability for outdoor use. They eliminate the need for water, making them ideal for locations with limited water availability.
- High Efficiency
- The finned design enhances the heat transfer rate, leading to high efficiency in dissipating heat. This makes Fin Fan Heat Exchangers preferable in applications where efficient cooling is paramount.
- Versatility in Applications
- Fin Fan Heat Exchangers find applications in various industries, including petrochemical, power generation, and manufacturing. Their versatility stems from the ability to handle a wide range of temperatures and pressures.
Considerations for Fin Fan Heat Exchanger Selection
- Environmental Factors
- The choice between natural and forced draft configurations depends on environmental factors such as wind conditions, temperature variations, and site-specific considerations.
- Material Selection
- The materials used in constructing Fin Fan Heat Exchangers must withstand the corrosive effects of the process fluid and environmental conditions. Common materials include aluminum, copper, and stainless steel.
- Maintenance Requirements
- Regular maintenance is essential for optimal performance. This includes cleaning the finned surfaces to prevent debris buildup and inspecting for any signs of wear or corrosion.
Applications of Fin Fan Heat Exchangers
- Petrochemical Industry
- Fin Fan Heat Exchangers play a vital role in cooling various processes within the petrochemical industry, including the condensation of hydrocarbons and cooling of gases.
- Power Generation
- Power plants utilize Fin Fan Heat Exchangers for cooling purposes, particularly in the condensation of steam in power generation cycles.
- Chemical Manufacturing
- In chemical manufacturing processes, these heat exchangers contribute to the temperature control of reactors and the condensation of volatile substances.
Understanding Fin Fan Heat Exchangers is essential for harnessing their benefits across industries. Their efficiency, versatility, and suitability for outdoor applications make them indispensable components in processes requiring effective heat dissipation. Whether in petrochemical, power generation, or manufacturing, Fin Fan Heat Exchangers contribute significantly to optimizing industrial operations.
Exploring Shell and Tube Heat Exchangers
Shell and Tube Heat Exchangers are integral components in various industrial processes, offering efficient heat transfer capabilities. Let’s delve into the key aspects that define their design, functionality, and applications.
Basic Structure and Design
- Tube Bundle Arrangement
- Shell and Tube Heat Exchangers consist of a cylindrical shell with a bundle of tubes running through it. The tubes can be arranged in different configurations, such as straight, U-shaped, or helical, depending on the application requirements.
- Tube Material and Size
- The material of the tubes is crucial for withstanding the corrosive effects of the process fluid. Common materials include stainless steel, copper, and titanium. The size and diameter of the tubes influence the heat transfer capacity of the exchanger.
- Baffles for Enhanced Heat Transfer
- Internal baffles within the shell guide the flow of the process fluid, promoting turbulence and enhancing heat transfer efficiency. Baffles prevent the fluid from taking a direct path through the exchanger, ensuring optimal heat exchange.
Key Features and Operation
- Counter flow and Parallel Flow Configurations
- Shell and Tube Heat Exchangers can operate in counter flow or parallel flow configurations. In counter flow, hot and cold fluids flow in opposite directions, maximizing temperature differences. Parallel flow involves both fluids moving in the same direction.
- Heat Transfer Mechanism
- Heat is transferred between the hot and cold fluids through the tube walls. This mechanism ensures efficient temperature exchange while keeping the two fluids physically separated.
- Versatility Across Industries
- Shell and Tube Heat Exchangers find applications in diverse industries, including chemical processing, HVAC systems, power generation, and refrigeration. Their versatility makes them suitable for various temperature and pressure requirements.
Advantages of Shell and Tube Heat Exchangers
- High Heat Transfer Efficiency
- The design of Shell and Tube Heat Exchangers allows for high heat transfer rates due to the large surface area provided by the tube bundle.
- Ability to Handle High Pressures and Temperatures
- These heat exchangers are well-suited for applications involving high pressures and temperatures, making them reliable in demanding industrial processes.
- Ease of Maintenance
- The tube bundle in Shell and Tube Heat Exchangers can be easily accessed for cleaning and maintenance. This accessibility contributes to their longevity and operational efficiency.
Considerations for Selection
- Fluid Properties
- The selection of Shell and Tube Heat Exchangers is influenced by the properties of the fluids involved, including their corrosiveness, viscosity, and thermal conductivity.
- Space Constraints
- The physical size and layout of the exchanger need to align with space considerations at the installation site. Shell and Tube Heat Exchangers are known for their compact designs, making them suitable for applications with limited space.
- Cost Considerations
- While highly efficient, the cost of Shell and Tube Heat Exchangers may vary based on materials, size, and design complexity. A careful cost-benefit analysis is essential for optimal investment.
Applications Across Industries
- Chemical Processing
- Shell and Tube Heat Exchangers are commonly used in chemical processing for heating, cooling, and condensation processes.
- Power Generation
- These heat exchangers play a critical role in power plants for cooling purposes, particularly in steam condensers.
- Refrigeration and HVAC
- The HVAC industry relies on Shell and Tube Heat Exchangers for air conditioning and refrigeration applications, ensuring efficient heat transfer.
Exploring Shell and Tube Heat Exchangers reveals their versatility, efficiency, and adaptability to various industrial settings. Whether in chemical processing, power generation, or HVAC systems, these heat exchangers continue to be integral components for optimizing heat transfer in diverse applications.
A Comparative Analysis
Distinguishing between Fin Fan and Shell and Tube Heat Exchangers is crucial for selecting the right option for specific needs. We’ll explore the differences between these two types, considering factors such as heat transfer efficiency, size, and complexity.
Factors Influencing Performance
Heat exchangers play a pivotal role in diverse industries, facilitating the efficient transfer of thermal energy between fluids. The performance of these crucial components is influenced by several factors, each of which plays a significant role in determining their effectiveness.
1. Temperature Requirements
- Optimal Operating Range: The temperature at which a heat exchanger operates directly impacts its efficiency. Understanding the specific temperature requirements of the process fluid and the desired output is essential for selecting the right heat exchanger.
- Heat Load Variations: Heat exchangers must be designed to handle variations in heat load. Changes in the temperature of the process fluid or the ambient temperature can impact the overall performance.
2. Space Considerations
- Physical Dimensions: The available space for installation is a critical factor. Some heat exchangers, such as compact designs or those with modular configurations, are better suited for installations with space constraints.
- Airflow and Ventilation: In the case of air-cooled heat exchangers, ensuring proper airflow and ventilation is crucial. Space considerations influence the choice between natural draft and forced draft configurations.
3. Maintenance and Operational Costs
- Material Durability: The material composition of heat exchangers affects their resistance to corrosion and wear. Selecting durable materials reduces maintenance needs and extends the operational lifespan.
- Cleaning and Accessibility: Regular maintenance is vital for sustained performance. Heat exchangers with accessible components and easy cleaning mechanisms contribute to lower operational costs.
4. Fluid Properties
- Corrosiveness: The corrosiveness of the process fluid determines the type of materials suitable for construction. Compatibility with the fluid’s properties ensures the longevity of the heat exchanger.
- Viscosity and Thermal Conductivity: Understanding the fluid’s viscosity and thermal conductivity helps in designing heat exchangers that can effectively transfer heat without compromising efficiency.
5. Flow Rate and Pressure Drop
- Flow Rate Optimization: Achieving the desired flow rate for both hot and cold fluids is crucial. Balancing the flow rates ensures efficient heat transfer and prevents issues like uneven temperature distribution.
- Pressure Drop Considerations: Minimizing pressure drops across the heat exchanger is essential for maintaining consistent flow and preventing system inefficiencies.
Considering these factors collectively and in tandem is essential for the proper selection, installation, and operation of heat exchangers in industrial processes. Each factor interacts with others, and a holistic approach ensures optimal performance and longevity.
Real-world Applications
To provide a practical perspective, we’ll explore real-world applications of Fin Fan and Shell and Tube Heat Exchangers across different industries. From petrochemical plants to power generation, these heat exchangers play a pivotal role in various processes.
Advancements in Heat Exchanger Technology
The field of heat exchanger technology is dynamic, witnessing continuous advancements. We’ll discuss recent innovations and improvements that enhance the efficiency and reliability of both Fin Fan and Shell and Tube Heat Exchangers.
Best Practices for Installation and Maintenance
Proper installation and regular maintenance are critical for ensuring the optimal performance and longevity of heat exchangers. This section will provide valuable tips and best practices for users and operators.
Case Studies
Examining successful case studies will highlight how companies have benefited from the use of Fin Fan and Shell and Tube Heat Exchangers. These examples will demonstrate the practical impact of choosing the right heat exchanger for specific applications.
Future Trends in Heat Exchanger Technology
Looking ahead, we’ll explore emerging trends and predictions in heat exchanger technology. Stay informed about the latest developments that could shape the future of these essential industrial components.
Conclusion
The world of heat exchangers is intricate, with the efficiency and longevity of these vital components reliant on a delicate balance of factors. From temperature requirements to spatial considerations, fluid properties, and maintenance costs, each element plays a crucial role in shaping the performance of heat exchangers.
A meticulous understanding of these factors enables industries to make informed decisions, ensuring the seamless operation of heat exchangers in diverse applications. As technology advances, continual consideration of these factors will pave the way for innovative solutions, optimizing heat transfer and contributing to the efficiency of industrial processes.
Editors Recommendations
- How to Connect Your AirPods to Xbox Series X
- How to Use AirTags: A Complete Guide
- How to link Fortnite Accounts on Xbox, PlayStation, and Switch
- How to get Fortnite on your Android Phone or Tablet
- How to Set Up WhatsApp Auto-Reply

Pooja Yadav is a Technical Content Specialist with over 6 years of experience. She mostly writes about the tech guides for Tech Hub Digital. She also has an interest in Smartphones, Bluetooth Earbuds/speakers, Wearables and all things gaming.
In her spare time, she watches movies, series and enjoys spending time outdoors.